Are you looking for industrial valve manufacturers and valve suppliers for your business pipeline? Yuanda Valve, is the world's leading valve manufacturer and supplier. We have different types of industrial valves such as check valves, control valves, fire valves, etc.
Industrial valves are mechanical devices that open, close, or partially block channels to regulate the flow of liquids or gases in a system. the global industrial valves market size was USD 73 billion in 2021 and is expected to reach USD 90.5 billion by 2026, and is projected to grow at a CAGR of 4.4% during the forecast period. Increasing demand for valves in healthcare and pharmaceutical industries due to the COVID-19 pandemic, the surge in demand for setting up new nuclear power plants and retrofitting existing ones, increasing demand for maintenance of connected networks and monitoring of industrial equipment, growing adoption of automation technologies in process industries, and growing focus on the development of smart cities across the globe are the key drivers of the industrial valves market.
There are many industrial valve manufacturers across the globe. They produce various types of industrial stock valves, each with unique features and applications, and it can be challenging to find one that will provide the best results in your particular application. As applications have become more specific and complex, valves have evolved into nine main types to suit different requirements. These nine types cover all industrial applications and services.
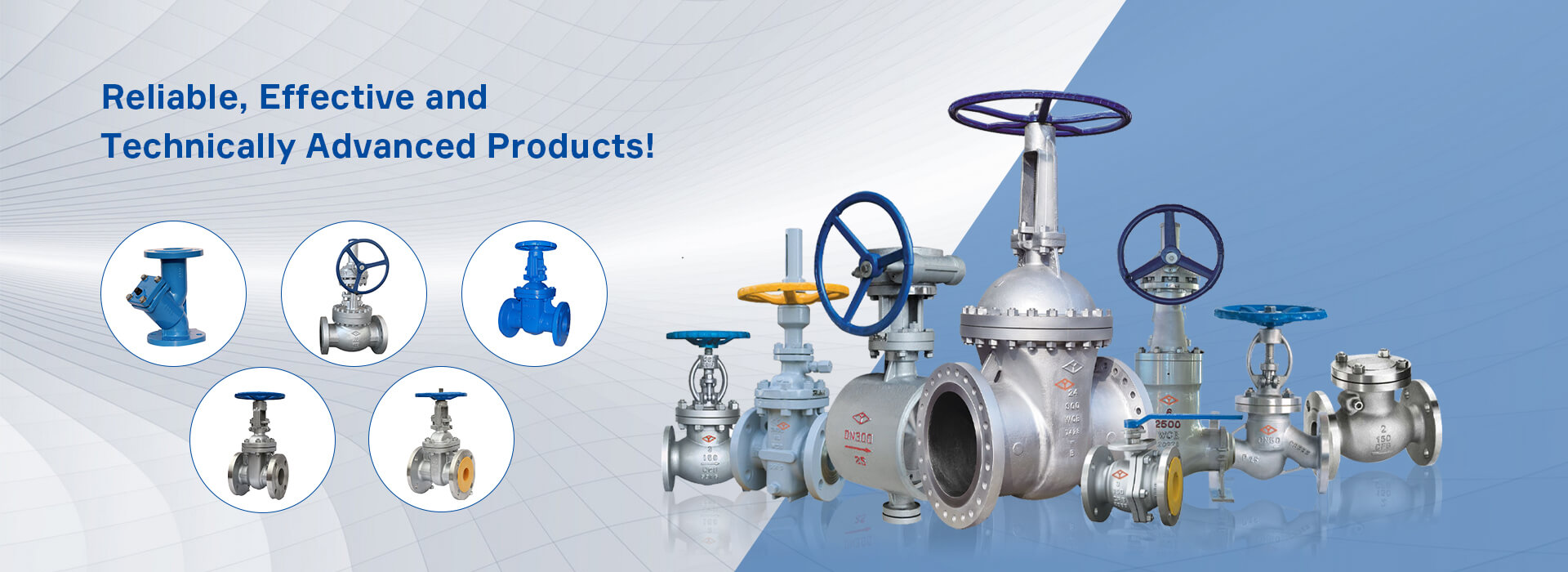
1. Gate valve
Gate valves are designed to be used as isolation valves. These valves help to control the flow of liquid through the pipeline. In order to start or stop the flow of water or any other type of liquid, these valves are fixed to the pipeline. Gate valves are used for various purposes and are commonly found in homes and commercial centers. Different materials such as stainless steel, cast iron, alloy steel, forged steel, etc. are used to manufacture these valves. Gate valve suppliers classify gate valve types into two main types: parallel and wedge valves.
Gate valves are used to stop or start the flow of water. The function of a gate valve includes lifting the round shape of a rectangular gate out of the fluid path. When the gate valve is open, there is nothing to impede the flow because the pipe diameter and the gate have the same opening. The valve size can be determined by this orifice diameter.
Advantages
- Gate valves have very low frictional losses
- They can be used in both directions in the circuit
- They provide laminar flow with minimal pressure loss
- Gate valves help save energy and reduce the total cost of ownership
Will have low-pressure drop when fully open and seal tightly
Applications
Gate valves are excellent shut-off/open valves for any application. They are suitable for wastewater applications and neutral liquids. Gases with a temperature range between -20°C and 70°C and a maximum pressure of 16 bar can be used with gate valves. Knife gate valves are used for slurry and powder media. 2.
Related news: The Working Principle And Features Of Cast Iron Gate Valve
2. Globe valve
Globe valves are one of the most popular types of valves for a variety of applications. These valves are similar to gate valves and use linear motion to throttle the flow. They are used to control the flow in the pipeline and are regulated by the position of the movable disc (or plug) relative to the fixed ring seat. The main advantage of a globe valve is that it does not leak like other valves.
A Globe valve consists of baffles that separate the inside of the pipe, which is usually parallel to the length of the pipe. They are named after their spherical body shape, with the two halves of the body separated by an internal baffle. It consists of a removable disc element and a fixed ring seat located inside a roughly spherical body.
Stop valves are available in three body designs: Z-body, Y-body, and angle valves, and three designs of valve plates: ball, composite, and plug.
Advantages
- Stop valves throttle the flow and have a good full shutoff.
- Shorter opening and closing times.
- Easier surface preparation of the valve body seat.
- They can be used as shut-off check valves.
- They contain positive shutoff
Applications
Shutoff valves are suitable for a variety of applications because of their ability to stop, start, and regulate flow. Typically, you will see them used for regulatory capacity, including but not limited to fuel systems, boiler and main steam vents and drains, and cooling water systems.
Related news: Gate Valve vs Globe Valve
3. Ball Valves
Ball valves are valves that use a ball to control the flow of material from one opening to the next. These valves work by allowing the orifice to open, block or partially open to regulate the flow of gas/liquid. Ball valves are ideal for use with gases because they provide a better seal. They are very versatile as they support pressures up to 700 bar and temperatures up to 200°C and typically range in size from 0.5 cm to 30 cm. They are simple in construction and easy to operate and maintain.
They are designed with special measures to allow only the 90-degree rotation required to open and close the ball valve. These valves are a remarkable industrial choice because they provide a reliable and gas-tight seal in a closed position.
Types of industrial ball valves include
CSA gas ball valves: Gas ball valves are a special type of ball valve that requires CSA (Canadian Standards Association) certification for safe use incombustible gas applications. Valves that are CSA certified have undergone rigorous quality testing in accordance with U.S. law and measures established by other independent organizations (UL, ANSI, NSF, etc.).
Express/EzGrip Ball Valves: EzPress and EzGrip ball valves are ergonomically designed to be easily and quickly activated or deactivated in industrial applications. These valve connections are designed to save time and money during installation.
PEX Valves: PEX valves are two-way, full-way, right-angle rotary valves most commonly used to shut off the water supply to plumbing fixtures and other equipment during repair or maintenance service. f-1960, f-1807, and Everloc + are the most common types of sex connections.
PP-R Valves: PP-R valves are designed to be compatible with PP-R piping, which is a straight, rigid, cylindrical pipe used to transfer a variety of fluids in industrial applications. the polypropylene composition of PP-R piping and valves makes them highly resistant to corrosive chemicals and abrasive particles. The system uses hot welding and electrofusion to make socket and butt weld connections.
Advantages
- They incorporate a compact and low-maintenance design that requires no lubrication
- Cost-effective among all valves
- The biggest advantage of ball valves is their poor throttling characteristics, which can cause the ball valve seat to be susceptible to erosion.
- They provide leak-proof service.
- They can be opened and closed quickly.
- Ball valves offer multi-way design flexibility.
Applications
Ball valves are commonly used in flow systems for ships, fire protection services and in the chlorine manufacturing industry. Ball valve suppliers say these valves can be used in a variety of applications and markets, such as gas processing, transmission and storage, and industry.
Related news: Advantages Of Brass Ball Valve
4. Butterfly Valves
Butterfly Valves Butterfly valves are designed to regulate flow but have limited control. The butterfly valve can be easily operated by turning the handle 90 degrees. It consists of a metal disc in the valve body positioned perpendicular to the fluid in the closed position. The flow of fluid can be regulated by rotating it in the middle. Butterfly valves are configured for electric, manual or pneumatic operation.
Butterfly valve suppliers say these valves are used in a wide range of applications such as water supply, wastewater treatment, fire and gas supply, as well as in the chemical and petroleum industries, fuel handling systems, power generation, etc. These valves can be operated by a handle, gear, or actuator depending on specific needs.
Advantages
- Butterfly valves are very precise, which gives them an advantage in industrial applications.
- They are very reliable and require little maintenance.
- They have the ability to throttle the flow.
- They can be installed or removed without dislocating the piping system
Applications
Butterfly valves are used in wastewater treatment plants, power plants and processing plants for shut-off regulation and isolation services, and are particularly popular in oversized diameter pipelines.
Also used in pharmaceutical, chemical and food processing
They are used for corrosive fluids at low temperatures and pressures.
Related news: Butterfly Valve Introduction Guide
5. Check Valves
Check Valves Check valves are also known as non-return valves (NRVs). They allow liquid to flow in one direction only and prevent the medium from flowing back in the opposite direction. The purpose of a check valve is to prevent process reversal in a system, which could damage equipment or disrupt the process.
They are typically used to protect pumps in liquid applications or compressors in gas systems where backflow may cause the pump or compressor to shut down. The basic design of check valves reduces backflow in the line.
Because of their simpler design, they can operate without human interaction and automation. They rely on the flow rate of the fluid to open and close. The higher the flow rate, the more the valve opens until it reaches its maximum fully open position.
Types of check valves include
Lift check valves: With lift check valves, the ball or piston opens at a specified pressure to allow fluid flow. A decrease in pressure will force the piston or ball into the seat, which closes the valve and prevents backflow.
Swing check valves: Swing check valves rely on an articulating disc that swings away from the seat to allow forward flow. If the upstream flow is stopped, the valve flap returns to the seat to prevent backflow.
Butterfly Check Valves: Butterfly check valves consist of two semi-circular gates hinged together. Forward flow pushes the gate open, while reverse flow retracts them.
Advantages
Simple design.
Effective in preventing backflow.
Can be used as a backup system.
Applications
Check valves are used in applications where backflow prevention is required, such as pumps and compressors. Check valves are commonly used for feed pumps in steam boilers. Check valves are also used in chemical plants and power plants with multiple processes. Check valves are also used when there are multiple gases in a pipeline.
Related news: Common Types Of Check Valves
6. Needle Valves
Needle valves are named for the needle-like shape of their discs. Needle valves have a long, conical needle-like point for relatively fine adjustment of fluid flow. They are sometimes used as components of other valves because the needle allows the size of the fluid flow opening to change gradually. The mechanism of action is similar to that of a globe valve. Needle valves provide greater precision and control in smaller piping systems. Still part of the quarter-turn series, needle valves function better at low flow rates.
Advantages
Efficient control of fluid media, suitable for finely regulated flows.
Ideal for vacuum service or any system requiring precision.
Minimal mechanical force is required to seal the valve.
Applications
Needle valves are used in instruments that require more complete control of fluid fluctuations and more precise fluid flow. Needle valves are more commonly used in calibration applications. They are also associated with distribution points in piping systems where needle valves are used as regulators of the media.
7. Pinch Valves
Pinch valves, also known as pinch valves, are another type of valve used for stop/start and throttling. A pinch valve consists of a sleeve molded from rubber or other synthetic material and a pinch mechanism. The pinch mechanism (stem or gate) is lowered onto the valve body to shut off the flow through the system. Pinch valves are part of the linear motion valve family. Linear motion allows the medium to flow unobstructed. The clamping mechanism of the clamping tube inside the valve serves to control the flow of fluid.
Advantages
Simple design with no internal moving parts.
Ideal for slurries and thicker, even corrosive media.
Helps prevent media contamination.
Low maintenance costs.
Applications
Pinch valves are primarily used for unrestricted fluid flow. They are best suited for slurry applications. Pinch valves are ideal for applications that require complete isolation from valve components and environmental contaminants.
Other applications that use pinch valves include wastewater treatment, chemical treatment, cement handling, etc.
8. Plug Valves
A rotary motion valve is used to stop and start fluid flow. Plug valves are part of the angle travel valve family. The disc acts as a gas-tight shutoff device and is located on a plug or cylinder. Due to its conical end and appropriately named plug valve. Its closing and opening mechanism is similar to that of a ball valve. The disc is a solid conical or cylindrical plug with a bored passage at right angles to the longitudinal axis of the plug. When open, the plug is aligned with the inlet and outlet of the valve body. The plug is either round or cylindrical with a taper.
Advantages
Simple mechanism.
Easy in-line maintenance.
Low-pressure drop.
Reliable, tight-sealing capability.
Quick opening or closing with just a quarter turn.
Applications
Plug valves are effective in tight closing and opening valves. There are many applications that use plug valves. These include natural gas pipelines, slurries, applications containing large amounts of debris, and high temperature and pressure applications.
These valves are well suited for wastewater systems. Plug valves are also well suited for highly abrasive and corrosive media because there is no contact between the media and the internal valve components.
9. Pressure Relief Valves
A pressure relief valve is a valve that relieves or limits pressure in a pipeline to maintain pressure balance and avoid buildup. It is sometimes mistakenly referred to as a pressure safety valve.
Its primary purpose is to protect equipment in the event of an overpressure event or to increase pressure in the event of a pressure drop. There is a predetermined pressure level and if the latter exceeds the preset level, the valve will release additional pressure.
Advantages
Can be used in all types of gas and liquid applications.
Can also be used for high pressure and high-temperature applications.
Cost-effective.
Applications
Pressure-reducing valves are effective when backpressure is not a major consideration. Pressure-reducing valves can be seen in boiler applications and pressure vessels.
In summary - choosing the right valve for your piping system
These are the 9 types of valves used in industry today. Some act as tight protection against leaks, while others make great throttling valves. The most important question to ask yourself when looking for a valve is what do you need the valve to do? Valves are an important use in any piping system. Whatever the requirements of your system, there is always a valve that will serve that purpose. By understanding each valve, it becomes easier to learn how to apply them to your industry. Industrial valves can be purchased from manufacturers worldwide at affordable prices.
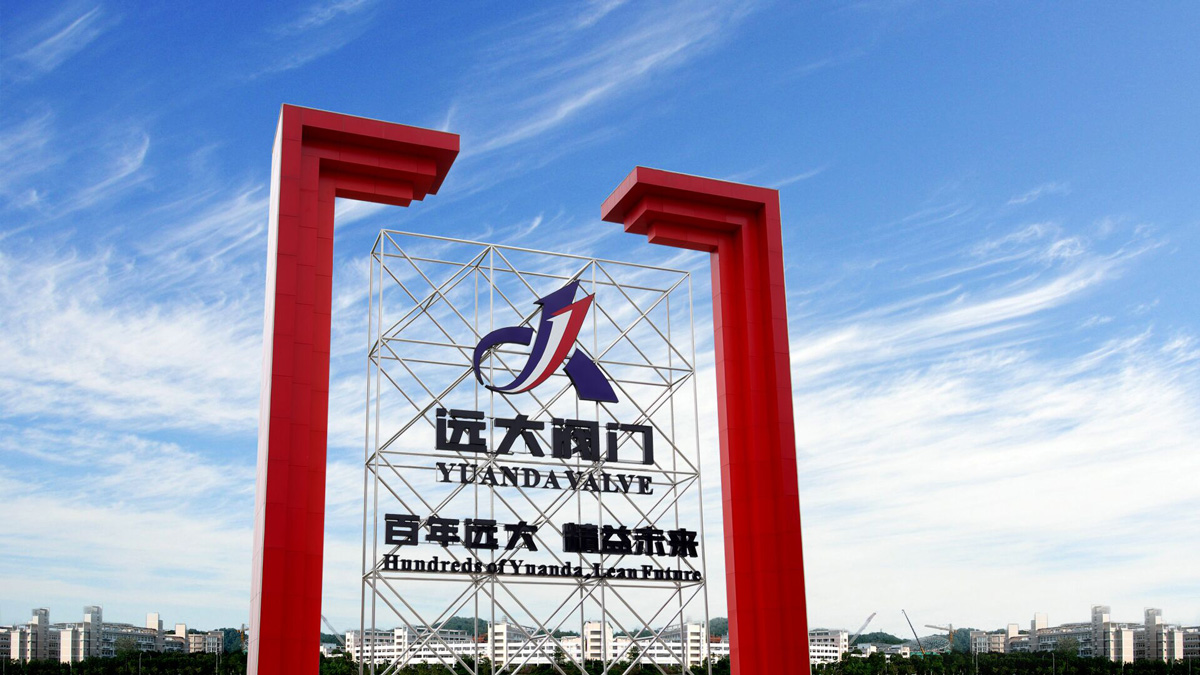
Are you looking for industrial valve manufacturers and valve suppliers for your business pipeline? Yuanda Valve is the world's leading valve manufacturer and supplier. We have different types of industrial valves such as check valves, control valves, fire valves, etc. Our valves are excellent in terms of packaging, dispatching and after-sales services and our uncompromising quality makes buyers contact us for future transactions. For more information, view www.yuandavalves.com.