When it comes to finding the right valve for your marine or industrial job, ball valves and butterfly valves often take center stage.
Contents:
• Understanding The Butterfly Valve
• Understanding The Ball Valve
• Ball Valves VS Butterfly Valves
• Selection Criteria
• Find The Right Valve for The Right Project
Understanding The Butterfly Valve
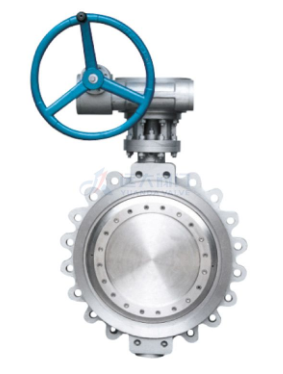
Butterfly Valve
A butterfly valve has a disc (E) driven by a lever or handwheel (A). When closed, the disc is perpendicular to the pipe flow direction. A seal (F) which seats within the valve body (D) ensures a tight closure with the valve disc. A butterfly valves valve characteristics are close to a linear relationship between the flow rate and the stem (C) position. The butterfly valve can be controlled manually, electrically, or pneumatically.
At larger diameters, butterfly valves are generally regarded as cheaper than ball valves. They have the least amount of parts and are relatively lightweight, requiring less support. The weight advantage of butterfly valves to ball valves can be significant at larger pipe diameters. There is a higher probability of leakage at high-pressure differences between the sides of a butterfly valve disc and the seal compared to a ball valve. Also, in applications with large pipe diameters, this high-pressure difference makes it difficult to open the valve, thereby requiring a bypass valve to balance both side’s pressure before the valve can be opened.
There is a pressure drop across the butterfly valve as the disc remains inside the flow even when fully open. This hinders using butterfly valves in process streams that need to be pigged, such as in the oil and gas industry. Butterfly valves are typically ON/OFF valves and are not suitable for precise fluid flow control.
Understanding The Ball Valve
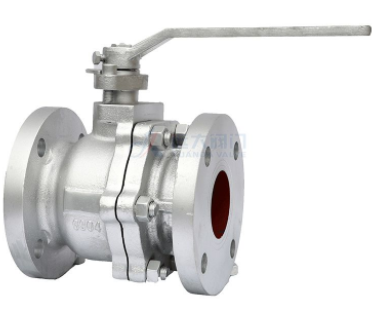
Ball Valve
A ball valve has a hollow spherical ball (F) that is pivoted at one or both ends. The top end of the ball is attached to a shaft (C), which is rotated by a handle (A) to change the valve position to open or close. When fully open, the hole in the ball lies parallel with the pipe flow direction. The ball rests on a seat (E) inside the valve body (G). The ball valve can be controlled manually, electrically, and pneumatically.
Ball valves can also have three-way or four-way flow directions in a T or L shaped bore. A ball valve’s flow characteristics can be read in our technical article on controlling fluid flow with ball valves.
The bore in a ball valve can vary from a size smaller than the pipe diameter (reduced port or reduced bore), a size equal to the pipe diameter (full port), or a V-port design. The design of the ball does affect flow characteristics. A ball valve can have a pressure drop across the valve in a reduced port ball valve or almost zero pressure drop in a full port ball valve, while a V-port design is ideal for stable flow control.
Unlike butterfly valves, ball valves have zero leakage when fully closed. The fluid pressure upstream of the valve pushes the ball against the seal, ensuring a positive shutoff position. Ball valves will easily open at a high-pressure difference on both sides of the valve and therefore do not require a pressure-balancing bypass.
Ball Valves VS Butterfly Valves
Several common features
ㆍThey are both quarter-turn rotary valves, which require a 90-degree rotation from opening to closing.
ㆍThese two materials are usually composed of cast iron, stainless steel, and brass.
ㆍEach valve effectively regulates the flow of most types of gases and liquids in a wide temperature range.
ㆍThey are relatively cheap, durable, and reliable.
ㆍBoth ball valves and butterfly valves are easily available through valve distributors.
These similarities do not mean the valves are interchangeable in all process functions. Instead, it suggests and corroborates why we need to take a closer look at the valves characteristics and what applications to use each valve. Let's take a look at the difference between ball valves and butterfly valves, and how they affect their use:
Differences
Design
Generally speaking, the ball valve is a ball with a hole. A butterfly valve usually consists of a disc mounted on a rotating shaft.
Features
When using a ball valve, turn the valve handle to block or partially block the hole on the ball or open the flow of gas or liquid through the valve. When using a butterfly valve, turning the valve handle turns the disk 90 degrees, to either fully open or fully block the flow of gas or liquid through the valve.
Pressure
One advantage of the ball valve is that it almost always rotates, no matter how much pressure is applied on the supply side. Once opened, the pressure hardly drops because the hole in the ball allows 100 percent of the gas or liquid to flow. The structure of the butterfly valve makes a part of the valve disc always interfere with the flow of liquid or gas. This means that when using a butterfly valve, there will always be a pressure drop. This also means that the butterfly valve may be difficult to open, and a bypass valve may be needed to create balance in the lines before the large butterfly valve can work properly.
Uses
Ball valves are more effective in sealing than butterfly valves, so ball valves are generally more suitable for projects involving the flow of gas. The cost of construction and maintenance of butterfly valves is usually low, so they are often used in large municipal water supply and sewer projects. They are also common in projects that control the flow of river or stream water.
Selection Criteria
The following criteria can be considered before selecting between a butterfly valve and a ball valve:
ㆍApplication: Butterfly valves are commonly used in water-based processes such as sewages, beer and soda production, etc. They are popular in chemical, agricultural, waste treatment plants, and food industries, partly because they are easy to clean. Ball valves can handle both liquid and gases with some solid particles (slurry). They are common in process plants, power plants, petroleum refining, oil, and gas exploration as they can be pigged for cleaning.
Flow capacity: Butterfly valves can provide a larger flow capacity as they are readily available at a larger pipe diameter than a ball valve.
ㆍSealing: Ball valves provide a tight seal in process applications that require zero leakages when shutoff.
ㆍOperating condition: Ball valves can operate up to 1,000 bar and 400 degrees Celsius. Butterfly valves typically operate at a lower pressure (less than 50 bar) and temperature (less than 250 degrees Celsius).
ㆍFlow regulation: Both valve types can be used for on/off control and proportional control, but ball valves are typically used for proportional due to better flow regulation.
ㆍPorts: A butterfly valve can only have two ports, while a ball valve can have more than two ports.
Find The Right Valve for The Right Project
Ball valves and butterfly valves are universal, relatively cheap, and can stand the test of time. Which one is suitable for which project depends on the size and scope of the task. If you need help determining whether a project requires ball valves, butterfly valves, or other types of valves, please contact a qualified valve distributor today.